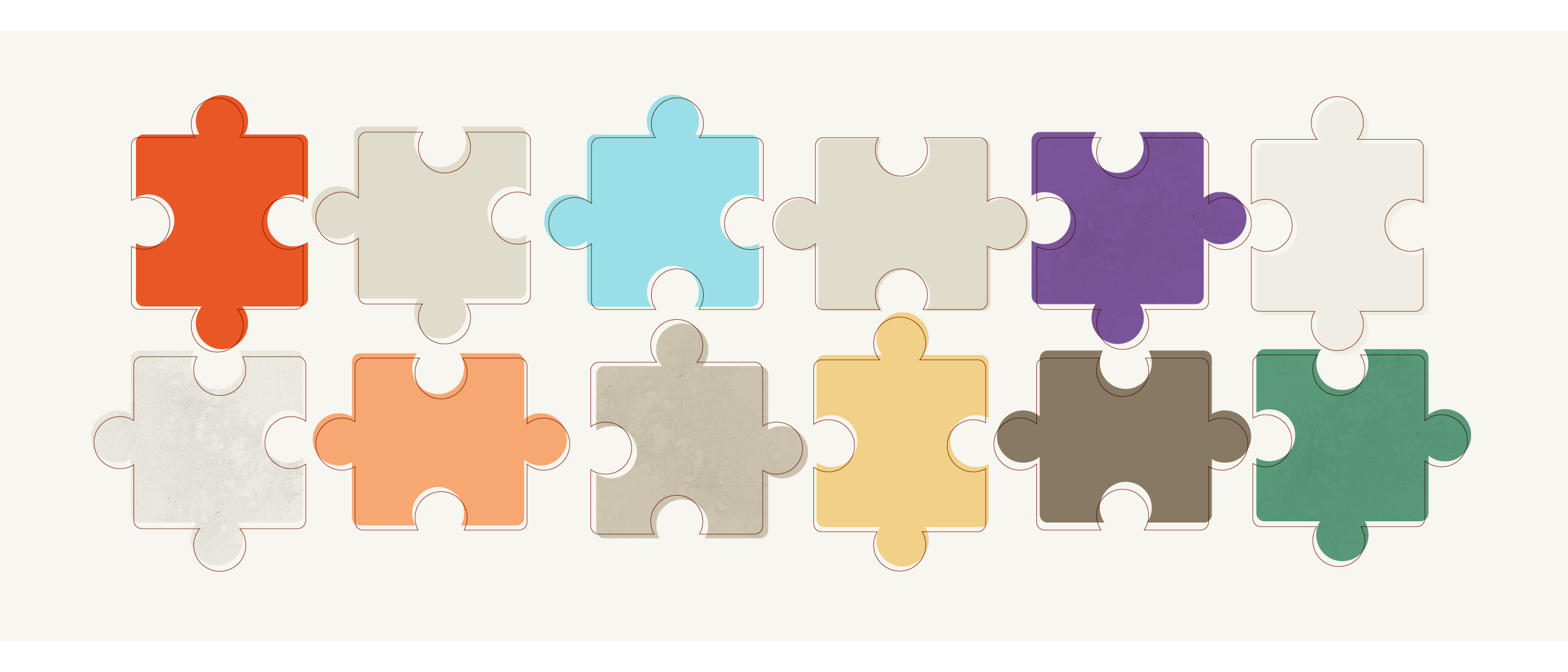
Celebrate, Advocate, Educate: Mineral Pride 2023
June 28, 2023Workplace Safety Training: 6 Things Employees Need to Know
June 30, 2023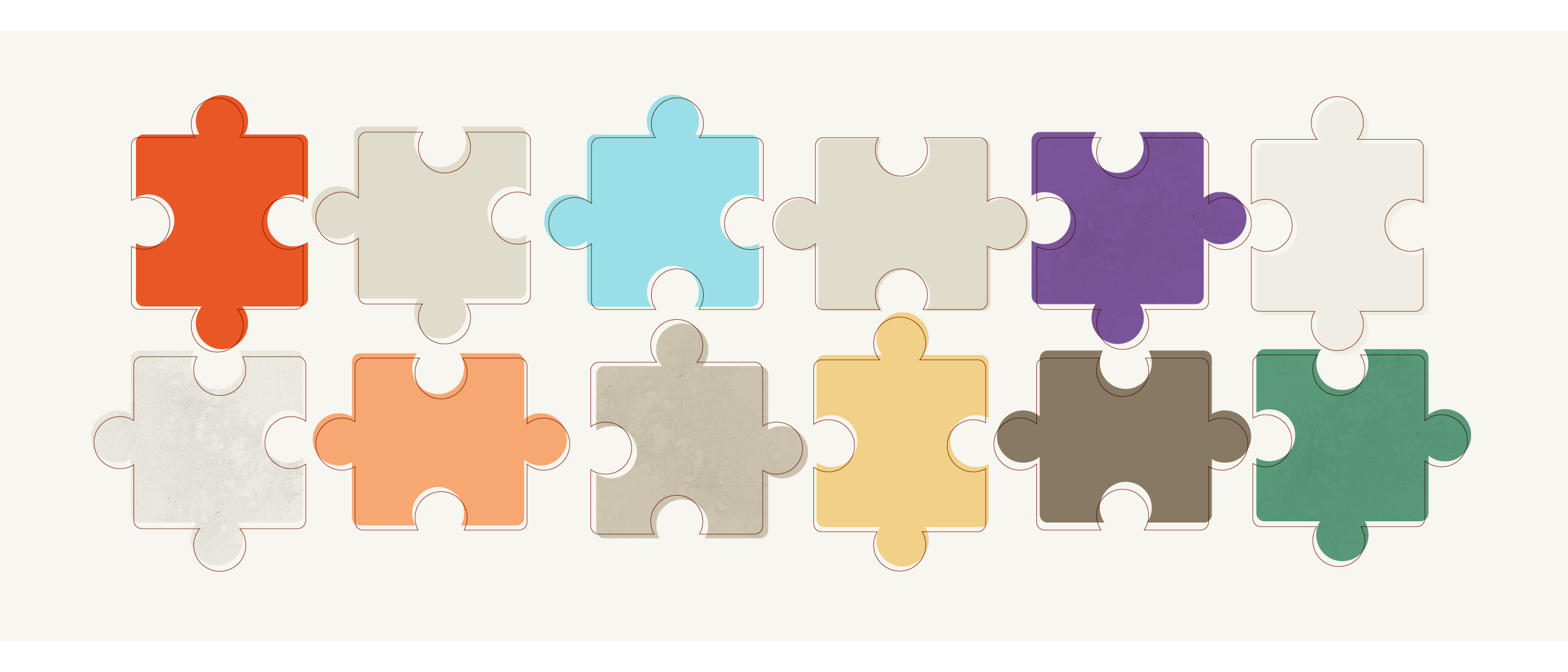
Celebrate, Advocate, Educate: Mineral Pride 2023
June 28, 2023Workplace Safety Training: 6 Things Employees Need to Know
June 30, 2023June is National Safety Month, annually sponsored by the Centers for Disease Control and Prevention to highlight efforts to prevent injury “in the workplace and any place.” At Mineral, helping our small business clients protect and maintain workplace safety is a key pillar to delivering on our mission to Elevate teams every day. In honor of National Safety Month, this post is the third in a multi-part series to aid small businesses in building and expanding a culture of safety.
Preventing, mitigating, and eliminating workplace safety incidents can feel like a game of whack-a-mole: As soon as you address one issue, another pops up. To shift from smashing problems reactively to solving them proactively, it’s helpful to have a framework for identifying where your greatest risks; that’s where a risk assessment comes in. A risk assessment, as it relates to workplace safety, is a method for identifying and evaluating potential hazards and risks that could cause harm to employees to provide a clear path forward in fulfilling your organizational safety mission and safety goals.
Conducting a risk assessment generally consists of eight steps. When you are ready to get started, the process outlined below will help ensure your assessment is comprehensive and effective.
1. Classify work areas and job tasks, and delineate those that most likely to result in a safety incident. Perhaps there is a history of incidents in one area or related to specific tasks. Consider where there is a lot of interaction with equipment and raw materials. Maybe there are areas or tasks that are more congested, undergoing change, or experience a lot of worker turnover. This step will help you select where improvement efforts are most needed and will be most effective.
For each work area or task, break each job into steps. For example, if you’re looking at a shipping area, you may break down the operation into goods staging, packing, and loading. Be sure to include any steps related to setup, cleanup, raw material or tool replacements, and shutdown to capture the entire work process and associated safety gaps. Also note the general frequency of each job step—i.e., once a shift, day, week, month or quarter.
2. Identify hazards. Once you have your work area, job steps and task frequency outlined, it’s time to think about what incidents might occur at each job step. At this point, it is critical to get input from multiple employees doing the work. Two heads are better than one in this instance because two people may perform a task differently, thus exposing different hazards at different work steps.
Throughout this step, consider the likelihood of cuts/lacerations, strains/sprains, caught-in/pinch points, burns, slips/trips, falls, awkward postures, chemical exposure, burns, crush/pressure, struck-by/against, fire, noise, electrical shock heat/cold, and inhalation hazards.
3. Categorize risk controls. For each hazard you identify, note how risk is controlled. There are three common categories of risk controls:
- Engineering controls. These are physical devices such as guards, barriers, safety switches, conveyors, lift equipment, carts, tools or other means of hazard prevention.
- Work practices and procedures. These are written or verbal policies used to prevent or manage hazards so they don’t result in injury. For example, training and the company norms for performing a task, are a means of control. However, consider if the work practices are consistent or if they vary from person to person. Often it is a lack of consistency that leads to different outcomes.
- Personal Protective Equipment (PPE). Note the types of PPE used for each task, including head, eye/face, ear, respiratory, skin and foot protection. Like work practices, consider if the PPE is used consistently by all employees who perform the job step.
4. Determine likelihood of negative outcomes. Commonly, likelihood criteria are listed as a four-point spectrum ranging from probable (no current risk controls in place), to likely, possible (inconsistently followed risk controls in place), and unlikely (consistently followed risk controls in place).
5. Evaluate hazard severity. Now that you have analyzed the adequacy of the controls in place to mitigate each hazard, determine the potential severity that the hazard prevents to employees. Severity criteria also can span a four-point spectrum, ranging from critical (life threatening or life altering injury— i.e., loss of life, limb, or key life function) to significant (serious but reversible injury, as in a burn or broken bone), marginal (minor reversible injury), and negligible (requires first aid only).
6. Characterize risk for each hazard. At this point, you are ready to make a risk determination for each hazard on your list, characterized as high, medium, or low. Using the equation below to assign numerical values (1-5 or 1-10) can be helpful in calculating risk determinations.
If F = frequency, L = likelihood, and S = Severity: Risk = FxLxS.
Low-risk hazards are considered those with acceptable risk or low priority for preventive or corrective action. Low risks usually have negligible or marginal severity, risk is carefully controlled, and/or the task is infrequently performed. High-risk hazards are usually those hazards with critical or significant severity rating and little or no risk controls for tasks that are frequently performed. Medium-risk hazards, natural, fall somewhere in between.
7. Take corrective and preventive action. Go back and look at your workplace safety hazard risks. Which ones are high? Prioritize these for corrective and preventive action to make the greatest positive impact on workplace safety. Set target dates and metrics for improvement, as well as which employee(s) are accountable for achieving said improvements. There may be some low-risk activities that can be corrected fairly easy at the same time, but stay focused on high-risk hazards first and foremost and work your way down the risk spectrum.
8. Review and reevaluate. As changes and improvements are made, go back and revise your risk assessment. Document what changes were implemented and re-evaluate the risks to ensure they are being mitigated effectively. Use the risk assessment as a working document to demonstrate your safety progress over time. It can be a great resource for communicating the lessons learned to leadership and employees and demonstrate how much effort is being put forth to ensure employees remain injury-free and the workplace is safe for all.
Risk assessment is an ongoing process that allows companies to continuously identify and evaluate new hazards and risks as they arise and make improvements over time. Use it as a foundation for your strategic improvement plan, setting safety goals and engaging your workplace toward the goal of eliminating workplace injuries.
Up next: Workplace safety training—what employees need to know.
The post 8 Steps to an Effective Safety Risk Assessment appeared first on Trust Mineral.